Thailand: TGI develops Smart Factory for Industry 4.0
The term “Industry 4.0” originates from the German government’s industrial evolution strategy unveiled in 2013 which promotes the computerisation of manufacturing, according to Mr. Varin Rodphothong, Director of Manufacturing Automation and Robotic Center, Thai-German Institute (TGI). The term is essentially equivalent to the “Internet of Things (IOT)” which has been circulating in the industrial sectors in recent years.
As for Thailand, the government’s vision of “Thailand 4.0” refers to modernisation of every sector in preparation for the Digital Era, including educational system, agriculture, environment, and industry.

A study by the Federation of Thai Industries (FTI) has shown that the Thai industrial sector is currently at the level of Industry 2.25. Several manufacturers have already evolved to Industry 4.0 level. Most are large conglomerates or multi-national corporations as integrating automation and robotics into the business requires quite large investment. Each company should understand the cost and revenue of automation and robotics to its business before investing.
The Director added that in entering Industry 4.0, manufacturers must upgrade to Smart Factory, which is the convergence of information and production. Information Technology (IT) in this era is digitalised and managed as a network or cyber net. Meanwhile, industrial production is digitalised to Industrial Automation. “Smart Factory” doesn’t necessarily mean human-less automation, but rather collaboration between humans and machines. However, human endeavours within the Smart Factory must be digitalised to work with machines. Radio-frequency identification (RFID) thus becomes more important as a tool to identify human activities and for recording, evaluating, and quality controlling processes. Handicraft businesses in which human resources is the fundamental component can become a Smart Factory by implementing sensor technology to make production processes more efficient.
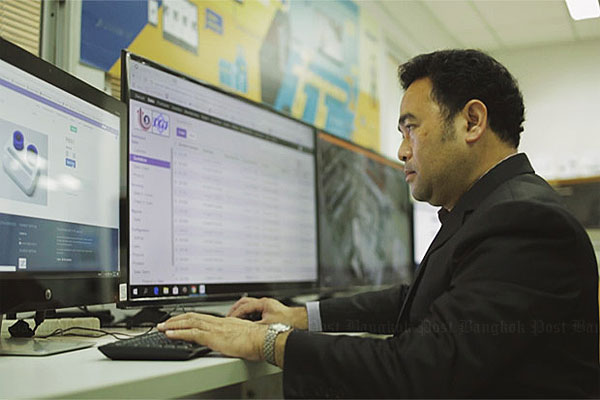
Smart Factory can also raise Thailand’s competitiveness in the global market. First and foremost, Thailand must develop Information Technology and turn conventional production into cyber production. Digital recording system, sensor system, and real-time data transfer are among the easier and lowest-cost improvements manufacturers can invest in and are a good start to achieving Cyber Physical Production System.
“Mr. Somwang Boonrakcharoen, President of TGI, has stated that the TGI is on a mission to help Thai manufacturers transform to Smart Factory for Industry 4.0. To this end, TGI established the Digital Manufacturing Centre specialised in Smart Factories. Inside the centre is a Smart Factory demonstration plant that business owners can visit and learn from. We also plan to build a smart factory for learning purposes. Thai-German Institute also offers advising services for smart factories, from designing systems to installing and training, to ensure smooth implementation of the whole system,” Mr. Varin concluded.